FTC Into the Deep: Tape Measure Inspired Our Level 3 Ascent
- Ronav Gupta
- Oct 24, 2024
- 5 min read
Updated: Oct 31, 2024

It all started on a typical evening, during one of our brainstorming sessions for FTC's INTO THE DEEP challenge. We were deep in discussion, tossing around various ideas for how our robot could successfully hang on Level 3 Ascent. We debated hooks, pulleys, winches—everything you can imagine. But nothing really seemed to click. The more we talked, the more it felt like we were overcomplicating the solution.
I remember I was holding a tape measure at the time, probably absentmindedly extending and retracting it while we worked. Suddenly, an idea hit me. "What if we used a tape measure?" I blurted out. Everyone stopped and looked at me like I had just suggested flying the robot to the moon. It seemed absurd at first, and the idea was quickly shot down.
Yet, the more we thought about it, the more intrigued we became. What if we could use a tape measure to assist with the climb? It’s compact, lightweight, and designed to extend and retract with precision. Over time, the skepticism started to fade, and the team’s curiosity grew. We realized that this "crazy" idea might actually be feasible. And so, we decided to prototype it.
From Concept to Prototype: Building the Tape Measure System
The first step was proving whether the tape measure could support the necessary weight. Our robot is estimated to weigh about 25 pounds, so we needed a solution that could not only extend vertically to reach the second rung but also bear that much weight without collapsing or breaking.
Step 1: The Prototype Build

We broke down a couple of standard tape measures, looking for the right length and strength. The challenge with most tape measures is that they are designed for horizontal use—they have to remain rigid when extended, but they're not built to support significant weight vertically. We needed something stronger than a regular tape measure but still lightweight.
To strengthen our setup, we attached a sturdy metal hook to one end of the tape, which would latch onto the Level 3 Ascent rung. On the opposite end, we screwed the tape into a couple of Sonic Hubs from GoBILDA. These hubs provided rotational motion, allowing us to extend and retract the tape measure using motors.
Step 2: Weight Testing
The critical test came when we mounted the tape measure assembly and began testing whether it could support the predicted weight of the robot. We progressively added weight, up to 25 pounds, and observed how the tape measure performed. To our surprise, the tape held up remarkably well, even under the stress of lifting the robot.
However, we had to ensure that the tape remained aligned throughout the extension and retraction process. A tape measure can easily bend or twist if it’s not properly guided, so we implemented a guide system to ensure smooth, controlled movement. This guide helped the tape extend vertically without bowing out or losing stability. By ensuring long standout, we kept the tape rigid as it reached upward, preventing it from collapsing.
Advantages Over Rigid Linear Actuators
As we explored various methods for our ascent mechanism, we realized that a rigid linear actuator pose a significant challenge when climbing to Level 3 Ascent. The issue arises when the robot transitions from the first rung to the second. With a linear actuator, the attachment point to the robot needs to be flexible, allowing for rotation, or else the actuator could get obstructed by the first rung during the ascent.
The attachment point to the robot needs to be flexible and allow for rotation as the robot ascends.
When a robot is climbing and moving from the first rung to the second, the trajectory isn’t perfectly vertical—there's an angle that naturally forms as the robot pulls itself up. This means that if the attachment point of the climbing mechanism (whether it's a linear actuator or, in our case, the tape measure) is rigid and doesn't allow for rotation, the first rung will act as an obstruction. The tape measure would not align properly, and the robot’s ascent could be halted or even damaged by this misalignment.
Rigid linear actuators extend in a straight line, and without a pivoting mechanism, the robot would collide with or get blocked by the first rung as the robot pulls itself upward. This would require careful alignment and additional engineering to allow for rotational flexibility at the attachment point—making the design more complicated and prone to failure.
However, the tape measure (or a nylon thread) avoids this issue. By design, a tape measure is flexible and can bend as needed. When the robot climbs, the tape measure can easily adjust its angle as the robot transitions from the first to the second rung. There’s no need for complex rotational mechanisms at the attachment point because the tape measure’s flexibility inherently accommodates the change in angle. This made it a perfect solution for the challenge.
Why the Tape Measure is Perfect for FTC's Level 3 Ascent

Now that we had successfully tested our prototype, we could dive deeper into why this system was not just a gimmick but actually well-suited to FTC's Level 3 Ascent challenge.
1. Compact Design
The tape measure's retractable nature makes it an ideal solution for FTC robots, where space is often a premium. When retracted, the tape takes up minimal space, leaving room for other essential components. When deployed, it extends several feet with ease, perfect for reaching the second rung of the ascent structure.
2. Precision Extension
One of the challenges with any hanging mechanism is controlling the ascent precisely. The tape measure, when paired with the Sonic Hubs and motors, gives us the ability to extend the hook to exactly the right length to reach the rung. There’s no guesswork—just smooth, controlled movement.
3. Weight Capacity
Although tape measures aren't typically designed for lifting, our testing showed that they can handle significant weight when properly reinforced. The guide system we implemented kept the tape measure aligned, ensuring it remained rigid even under load. This allowed it to reliably lift our 25-pound robot without collapsing or bending out of shape.
4. Simplicity of Integration
A big advantage of the tape measure solution is its simplicity. Unlike complicated pulley systems or linear actuators, the tape measure system is relatively easy to build and maintain. It also interfaces seamlessly with the motors and hubs from GoBILDA, making it easier to program and control.
5. Cost-Effectiveness
Another factor that made the tape measure approach appealing is its cost. Linear actuators and other sophisticated climbing mechanisms can be expensive, but tape measures are inexpensive and easy to replace. This gave us room in the budget to focus on other robot features without compromising on our ascent mechanism.
Next Steps: Fine-Tuning and Competition
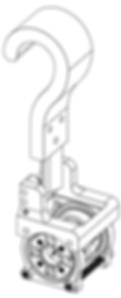
Our tape measure ascent system has gone from a wild idea to a working prototype, but we’re not done yet. There are still refinements to be made—optimizing the motor control, ensuring the guide system remains smooth under high load, and possibly testing different tape measures for even greater strength and flexibility.
But what started as an idea everyone laughed at has now become one of the most exciting features of our robot. I guess, sometimes, the most innovative ideas come from the least likely places. Who would have thought that a simple tape measure could be the key to mastering the Level 3 ascent in FTC's INTO THE DEEP challenge?
We’re excited to see how it performs in competition, and we’ll continue to push the boundaries of what's possible with this unconventional approach. Stay tuned for updates as we refine and perfect this mechanism—there’s much more to come!
A Message to All FTC Teams: Let's Talk Tape Measures!
If you’re part of an FTC team and you're considering using a tape measure in your ascent mechanism—or even just curious about the concept—we’d love to hear from you! Our team has learned a lot through trial and error, and we’d be more than happy to share more tips, insights, and lessons learned.
Feel free to reach out, and let’s innovate together!